硅溶膠精密鑄造是一種少切削或無切削的鑄造工藝,要提高其生產(chǎn)效率,可以從優(yōu)化工藝流程、設(shè)備升級改造、人員管理與培訓(xùn)等多方面入手,以下是具體方法:
- 優(yōu)化制殼工藝
- 調(diào)整硅溶膠性能:對硅溶膠的濃度、粘度、PH 值等參數(shù)進行精確控制和優(yōu)化。合適的硅溶膠性能可以加快干燥速度,減少制殼層數(shù)和時間。比如通過試驗確定較佳的硅溶膠濃度,使型殼干燥時間縮短,同時保證型殼強度。
- 采用高效干燥設(shè)備:升級干燥設(shè)備,如使用熱風(fēng)循環(huán)干燥爐、真空干燥設(shè)備等,能夠加快型殼干燥速度。合理控制干燥溫度、濕度和風(fēng)速等參數(shù),確保型殼均勻干燥,減少干燥時間。比如,采用智能控溫控濕的干燥設(shè)備,可使干燥時間縮短 30% 以上。
- 改進撒砂工藝:選擇合適的撒砂設(shè)備和砂粒,確保撒砂均勻且緊密。采用自動化撒砂設(shè)備,能夠提高撒砂效率和質(zhì)量,減少型殼制作時間。
- 熔煉與澆注優(yōu)化
- 選擇優(yōu)質(zhì)熔煉設(shè)備:先進的熔煉爐,如中頻感應(yīng)電爐,能夠提高熔煉速度和金屬液質(zhì)量。精確控制熔煉溫度和時間,減少熔煉過程中的能耗和雜質(zhì)產(chǎn)生,提高金屬液的純凈度和流動性。
- 優(yōu)化澆注系統(tǒng):設(shè)計合理的澆注系統(tǒng),包括澆口杯、直澆道、橫澆道和內(nèi)澆道的尺寸和形狀,以確保金屬液能夠快速、平穩(wěn)地填充型腔。采用底注式澆注系統(tǒng)或負壓澆注技術(shù),可以減少金屬液的氧化和氣孔缺陷,提高鑄件質(zhì)量和澆注速度。
- 設(shè)備升級與自動化
- 自動化制殼生產(chǎn)線:引入自動化制殼生產(chǎn)線,實現(xiàn)制殼過程的自動化操作,包括浸涂、撒砂、干燥等工序。自動化生產(chǎn)線可以提高生產(chǎn)效率,減少人為因素對產(chǎn)品質(zhì)量的影響,同時降低勞動強度。
- 智能檢測設(shè)備:使用智能檢測設(shè)備,如光學(xué)掃描儀、X 射線探傷儀等,對型殼和鑄件進行快速、準確的檢測。及時發(fā)現(xiàn)缺陷并進行修復(fù)或報廢處理,避免后續(xù)工序的浪費,提高生產(chǎn)效率。
- 人員管理與培訓(xùn)
- 提高員工技能水平:定期組織員工進行技能培訓(xùn),提高員工對硅溶膠精密鑄造工藝和設(shè)備的操作熟練程度。通過培訓(xùn),員工能夠更好地掌握工藝參數(shù)的控制和設(shè)備的維護,減少生產(chǎn)過程中的失誤和廢品率。
- 優(yōu)化生產(chǎn)組織與調(diào)度:合理安排生產(chǎn)計劃,優(yōu)化生產(chǎn)流程,減少生產(chǎn)過程中的等待時間和物料搬運時間。采用先進的生產(chǎn)管理系統(tǒng),實時監(jiān)控生產(chǎn)進度和設(shè)備狀態(tài),及時調(diào)整生產(chǎn)計劃,確保生產(chǎn)的連續(xù)性和高效性。
- 質(zhì)量控制與持續(xù)改進
- 建立質(zhì)量追溯體系:建立完善的質(zhì)量追溯體系,對原材料、生產(chǎn)過程和成品進行全程跟蹤和記錄。一旦出現(xiàn)質(zhì)量問題,能夠迅速追溯到問題的根源,采取有效的糾正措施,避免類似問題的再次發(fā)生。
- 持續(xù)改進生產(chǎn)工藝:定期對生產(chǎn)工藝進行評估和改進,通過試驗和數(shù)據(jù)分析,不斷優(yōu)化工藝參數(shù)和生產(chǎn)流程。鼓勵員工提出改進建議,對有價值的建議給予獎勵,促進生產(chǎn)效率的持續(xù)提高。
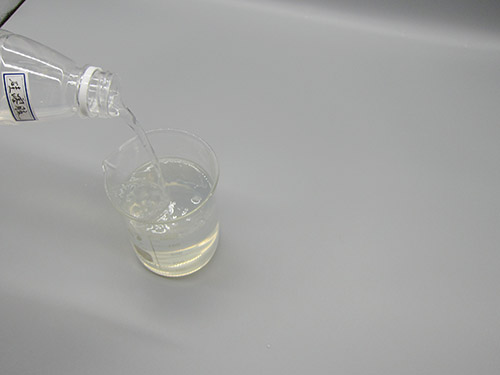